Dymond Engineering & Metal Products Ltd
Solid welds are crucial to the strength and appearance of your product. Dymond Engineering’s accomplished welders use TIG, MIG and spot techniques (described below) to produce visually discreet joins. Some joins when painted even appear invisible.
TIG Welding
TIG or ‘tungsten inert gas’: A tungsten electrode creates an electric arc, heating the metal being joined. Inert gas (usually Argon) protects the weld from oxidisation and contaminants.
Our skilled welders use TIG welding to achieve exceptionally smooth finishes and the high strength required for longevity in both mild steel and stainless steel products. TIG welds are neater and smoother than MIG, although evidence of the weld is always visible at the join.
MIG Welding
MIG or ‘metal inert gas’: An electrode creates an arc of intense heat, causing a significant amount of metal to melt and merge together. Further material is also added when the electrode melts, also becoming molten. It creates stronger welds than the TIG method (brilliant for longevity), that are more consistent and quicker to achieve – thus lowering the cost. When a fine finish is required MIG welds are ground down, making them flush. Used for both mild steel and stainless steel.
Spot Welding
A spot weld is rapid, taking less than a second to complete and leaves an unobtrusive mark – used for sheet metal and wire. How? Two bits of metal are clamped together with copper electrodes either side. When the electrodes are pushed together the join between the metal become the point of highest resistance to the electrical current flowing through. The metal in the join melts, and combined with some pressure a weld is achieved.
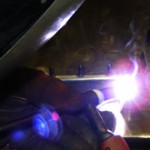
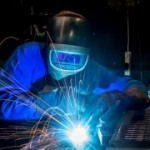
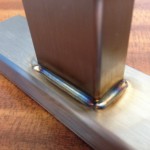
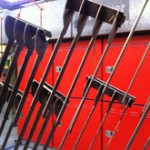